The how and when of technical commissioning
Jan 23, 2014
Technical commissioning is the cornerstone of high-quality building planning. With an objective understanding of a building’s systems, technical commissioning provides stakeholders not only the peace of mind that there is no impending catastrophe, but also an in-depth, behind-the-scenes look at how to improve efficiency.
However important, technical commissioning can seem convoluted and foreign to non-engineers. Being an astute building manager doesn’t mean being a commissioning expert – it just means being able to provide your technical commissioning specialist with the right information so he or she can hit the ground running.
The “how”: meter everything
This oftentimes goes overlooked because it is seen as a trivial luxury. Technical commissioning relies on an expert’s ability to take note of what’s going on all over the facility – from HVAC and overall electricity supply to how well the toilets are flushing. Installing meters to gauge the efficiency and output of the various devices around the structure greatly reduces the headache associated with commissioning. With sufficient metering, the task as a whole becomes cheaper, faster and more accurate.
No two buildings are exactly the same and not even the most seasoned expert can estimate how a structure is faring without reading instruments. A building is a unique amalgam of chillers, heaters, plumbing, electricity and about 1,000 other precise, specific systems that function well only when in a precarious state of balance.
Aside from just their use in the commissioning atmosphere, meters are monumentally important when simply understanding what’s happening (or not happening) on a daily basis at a building. Not having devices metered is equivalent to driving with your eyes closed – it lacks that all-too-important feedback.
The “when”: a perfect time does exist…
…and this epoch starts when the construction of a facility is just starting to wrap up and ends some time after the operability is in full swing. Ideally, it’s best to kick off technical commissioning in the construction phase because there’s still easy access to most of the systems and their components. There are few things more embarrassing (or expensive) than having to rip out an entire network of ducts or cables to reinstall something that was supposed to work the first time.
The commissioning should last up through the ribbon cutting of the building and measurements should reflect how the building handles its role as a fully functional, populated workplace. Oftentimes, system demands will spike during certain hours or work in a way previously not predicted by the initial planners.
Note that technical commissioning needs to be reserved and organized well before the ideal window described above. Ideally a technical commissioning official will be kept clued in throughout the undertaking; it’s only when the construction phase starts to conclude will he or she actually start to play a relatively active role.
It’s also worth stating that it’s never too late for technical commissioning, and any time is better than never. Even if your building is completely finished and functional, there is still amazing information waiting to be unlocked from the commissioning process.
To learn more about technical commissioning and how sys-tek can help make your facility more energy efficient, contact us.
Learn more about Commissioning in these other posts:
- Technical vs. Process Commissioning
- The Commissioning and Retro-Commissioning Process
- The Importance of Owner Involvement in Retro-Commissioning
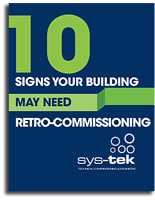
10 Signs Your Building May Need Retrocommissioning
If your building is exhibiting any of these key signs, you may be able to improve energy efficiency and reduce costs through RBCx.